Your telescope's motor tracking issues typically come from five main problems: mechanical failures like worn gears or backlash, improper polar alignment, unstable power supply, poor calibration, or environmental factors affecting performance. You'll need to check your mount's balance, guarantee proper voltage (ideally 12-14V), verify gear meshing, and confirm accurate polar alignment. A systematic approach to identifying and fixing these common issues will get your scope tracking the stars smoothly again.
Understanding Basic Tracking Mechanics
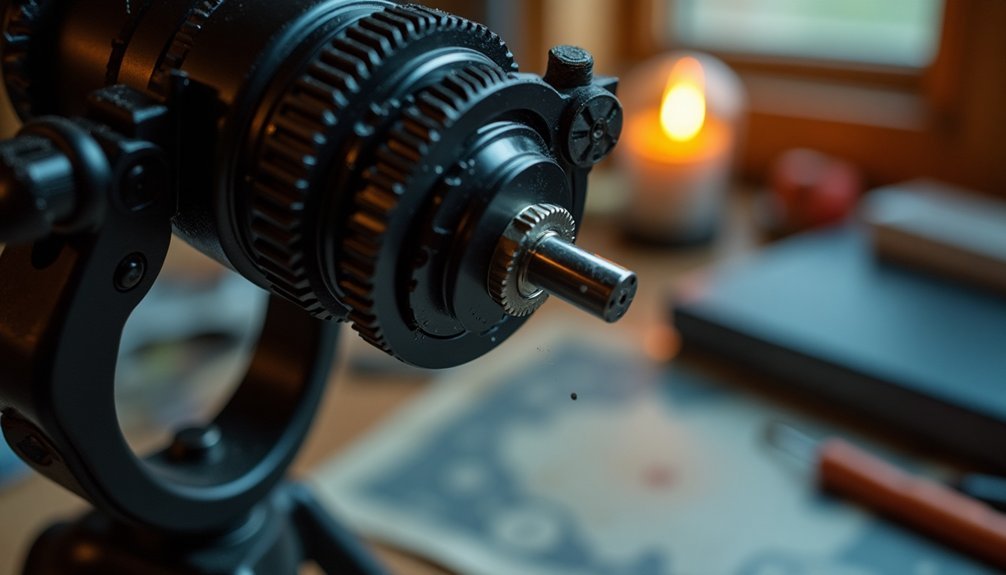
While telescope tracking may seem complex at first glance, it relies on fundamental mechanical principles that work together to follow celestial objects across the sky.
Your telescope uses specific drive types, including worm gears, spur gears, or friction drives, each serving unique tracking purposes. Traditional worm gears are popular because they offer 360:1 gear ratios.
To track objects accurately, your telescope needs precise positioning through high-resolution encoders and must maintain proper velocity control for both quick positioning and smooth tracking.
Accurate celestial tracking demands both precise encoder positioning and careful velocity management to ensure seamless astronomical observation.
The mount's coordinate system, particularly equatorial mounts, helps simplify the tracking process by aligning with Earth's rotation.
Your telescope's dynamic response – how quickly it reacts to position changes – depends heavily on the gearing system's stiffness.
Understanding these basic mechanics can help you identify why your telescope mightn't be tracking as expected.
Common Mechanical Failures and Solutions
When mechanical failures occur in telescope tracking systems, they often manifest through specific symptoms that you can diagnose and fix. Worn or loose gears typically cause backlash, resulting in delayed movement and inaccurate tracking. You'll notice this problem when your telescope fails to smoothly shift during direction changes.
To address these issues, start by checking your mount's balance and ensuring proper tension in clutches. Precise worm-driven gears can significantly reduce tracking errors in modern telescope mounts. If you're experiencing tracking errors, examine your gears for excessive play and tighten any loose components.
Don't forget to implement anti-backlash features through firmware adjustments. Regular maintenance, including cleaning and component checks, will prevent many common failures.
For persistent problems, you might need to upgrade faulty parts or streamline your setup by reducing mechanical stress from cables and accessories.
Proper Polar Alignment Techniques
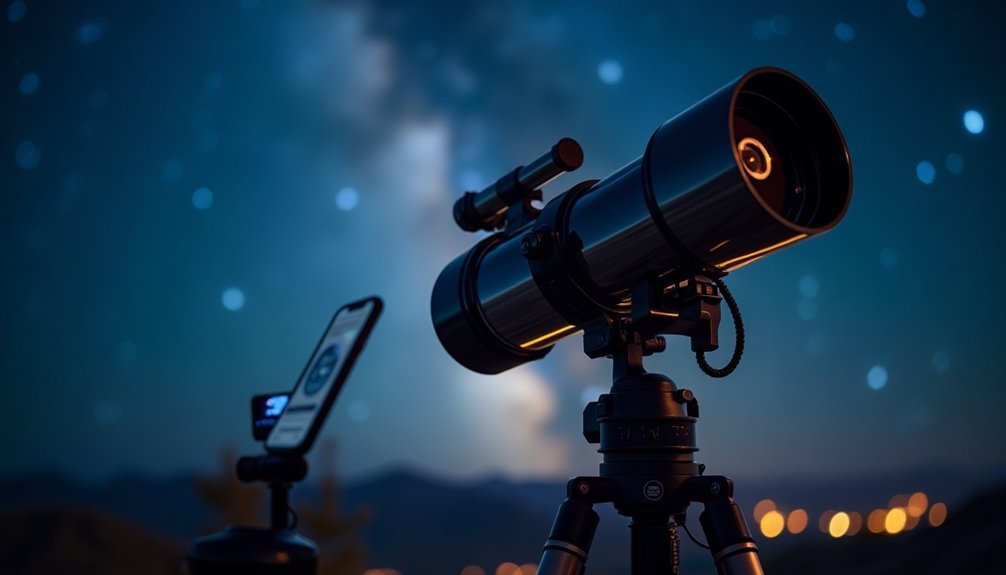
To achieve accurate tracking, you'll need to master the star drift method by observing how stars move and making precise altitude adjustments to your mount.
Your polar scope offers a quicker alignment solution, letting you align directly with Polaris or Sigma Octantis depending on your hemisphere.
Both techniques require careful attention to your mount's altitude axis, which you can fine-tune using the mount's adjustment knobs until stars maintain their position in your eyepiece. For optimal alignment precision, observe your target star's movement for 30 to 60 minutes to ensure proper tracking stability.
Basic Star Drift Method
Precision in polar alignment stands as a cornerstone of successful astronomical observation. Using the star drift method, you'll need to choose two specific stars: one near the meridian and another near the eastern horizon, both close to the celestial equator. A strong powered eyepiece will provide better visibility during the alignment process.
Drift Direction | Mount Position | Required Adjustment |
---|---|---|
South at Meridian | Too Far East | Move West |
North at Meridian | Too Far West | Move East |
South at East | Mount Too Low | Raise Mount |
North at East | Mount Too High | Lower Mount |
No Drift | Properly Aligned | None Needed |
Center your chosen star in a reticle eyepiece and observe its movement for at least five minutes. If you notice drift, make necessary adjustments to your mount's position. You'll need to repeat this process until the star shows minimal to no drift, ensuring proper tracking for your observations.
Altitude Axis Adjustments
Achieving proper polar alignment requires mastering the telescope's altitude axis adjustments.
You'll need to match your mount's altitude setting to your geographical latitude while ensuring your counterweights are properly balanced. This critical step prevents unwanted star drift during long exposure astrophotography.
Start by using online tools to determine your exact latitude, then adjust your mount's altitude screws accordingly. If you're using longer focal lengths or high magnification, you'll need even more precise alignment.
Center Polaris in your finder scope and make fine adjustments using the mount's altitude controls. Don't forget to securely clamp both axes after alignment to prevent movement. Checking for declination drift direction will help determine if your polar axis needs further east or west adjustments.
For challenging locations where Polaris isn't visible, you may need alternative alignment methods.
Remember that weather conditions and site obstructions can affect your alignment accuracy.
Polar Scope Techniques
Proper polar alignment through a polarscope represents one of the most reliable methods for precise telescope tracking. You'll achieve the best results by using a specialized reticle designed for seasonal compensation, along with digital apps that help fine-tune your adjustments. Magnetic declination adjustments must be considered when using a compass during initial setup.
Technique | Tool Required | Accuracy Level |
---|---|---|
Visual Centering | Reticle Pattern | Good |
Digital Assistance | Smartphone Apps | Better |
Star Positioning | Star Charts | Best |
Seasonal Compensation | Digital Reticle | Excellent |
To maximize your polarscope's effectiveness, center Polaris or specific stars in the reticle pattern while making small adjustments. Many modern polarscopes now integrate with digital apps that guide you through the alignment process. When properly executed, you can achieve alignment precision within an arc minute, ensuring your telescope's motor tracking performs efficiently throughout your observing session.
Motor Calibration and Testing
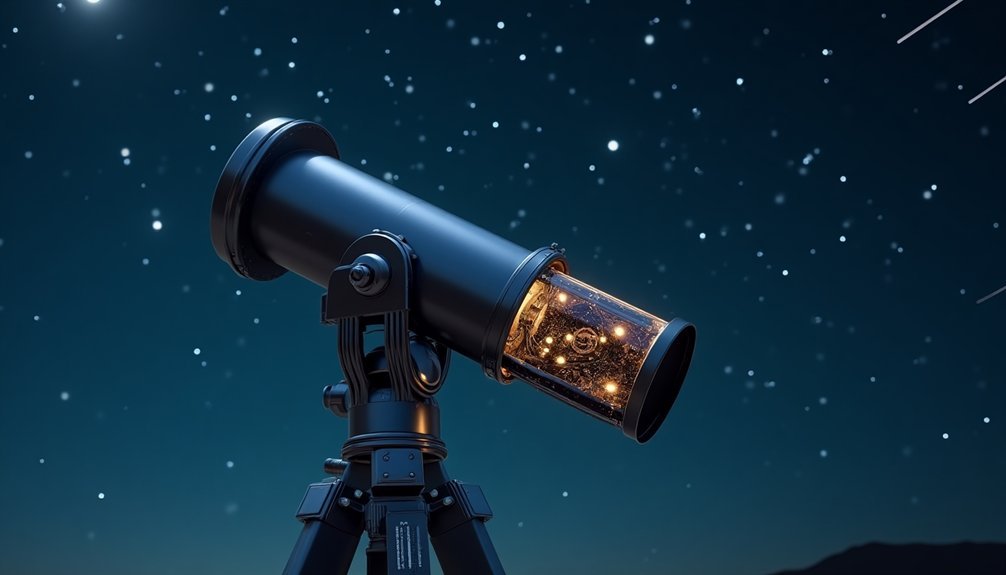
When you're troubleshooting telescope tracking problems, start by testing your motor's basic functions using the Clearline Calibration Tool to check signal duty cycles and encoder responses.
You'll need to verify that your power source remains stable and that your encoders are properly counting motor shaft rotations to maintain accurate tracking rates. The calibration tool uses color LED indicators to show when proper signal levels are achieved.
After confirming these fundamentals, you can fine-tune your drive system's accuracy by adjusting gear ratios and running automated calibration routines to eliminate any backlash or mechanical discrepancies.
Basic Motor Testing Steps
Motor testing requires five fundamental steps to guarantee reliable telescope tracking performance.
First, prepare your equipment by checking calibration settings and updating any necessary software.
Second, set up your test environment by verifying operational safety and ensuring all systems are ready.
Third, gather your essential test equipment, including a multimeter and appropriate power supply.
Fourth, collect accurate voltage and current data while running your motor through its paces. Don't forget to monitor both clockwise and counterclockwise rotation using your motor driver's directional controls.
Finally, analyze your test data to identify any irregularities in performance.
You'll want to use proper microstepping settings (typically 1/16) and maintain clean cable management throughout the process.
Remember to keep decoupling capacitors in place to minimize electrical noise that could affect tracking accuracy.
The Arduino Nano controls the stepper motors for precise movement during testing and operation.
Calibrating Drive System Accuracy
Since accurate drive system calibration forms the foundation of reliable telescope tracking, you'll need to master several key adjustment procedures.
Start by checking your encoder positioning and ensuring it's properly mounted on the motor shaft. Testing should confirm motors turn in the proper direction – if not, consider switching motor wires to resolve directional issues. You'll need to calibrate both motor speed and encoder ratios to match your telescope's gear system.
Watch for common issues like runaway motors or directional confusion, which often stem from improper duty cycle settings. If you're switching between battery and AC power, recalibrate your system to accommodate the power source change.
Use specialized tools like the Clearline Calibrator to adjust signal duty cycles to 50% for peak performance.
Don't forget to compensate for backlash in your gearing system, as this affects tracking accuracy when the telescope changes direction.
Power Supply Requirements
As telescopes become increasingly sophisticated, proper power supply requirements remain critical for reliable tracking performance. Your mount needs a stable 12V DC power source, though many systems perform at peak efficiency at 14V. Dropping below 12 volts at 1A can cause tracking failures and potential damage to voltage regulators.
Modern telescope performance depends heavily on stable power delivery, with most mounts requiring 12-14V DC for optimal tracking accuracy.
You'll need to account for voltage drops from cable resistance, especially with longer setups. Choose a power source that matches your needs – regulated AC adapters work well for home use, while field batteries with voltage regulators suit portable setups.
Don't forget to calculate your total power consumption, including all accessories like cameras and heaters. You'll want larger gauge cables to minimize voltage drops, particularly for high-power configurations.
Use proper grounding and shielded cables to reduce electromagnetic interference. For safety, make sure your power supply includes protection against overcurrent, overcharge, and undervoltage conditions.
Essential Software Settings
You'll need to properly configure your mount initialization protocols to guarantee your telescope accurately recognizes its starting position and calibration points.
To optimize tracking performance, set up your tracking algorithms with appropriate PID values and guiding parameters that match your specific mount's characteristics.
Keep your telescope's software and object databases current by establishing a regular update schedule, which helps maintain tracking accuracy and access to the latest celestial object data.
Mount Initialization Protocols
When setting up your telescope mount, proper initialization protocols are critical for guaranteeing accurate tracking and reliable performance.
You'll need to start by placing your mount in a designated park position and following a specific power-up sequence before connecting any control software.
- Connect your primary control software (like APCC) first, then establish secondary connections through the AP V2 ASCOM driver.
- Select your observing location and perform the "New Setup" process if you're initializing for the first time.
- Use the N S E W buttons to center your target before executing a ReCal for precise positioning.
Always verify your mount is powered up before launching any software, and confirm that your virtual COM ports don't conflict with existing serial connections.
Maintain regular updates of your AP V2 ASCOM driver to access the latest features and fixes.
Tracking Algorithm Configuration
Building upon proper mount initialization, successful tracking requires careful configuration of your software's algorithm settings.
You'll need to optimize several key parameters to achieve reliable tracking performance. Start by adjusting your minimum and maximum move times to prevent both unnecessary corrections and potential overshoots. Set your aggressiveness calibration carefully – too high and you'll overshoot, too low and corrections will lag.
Your guide exposure duration needs to balance quick response times with clear star images. Don't forget to implement dithering between exposures to reduce pattern noise.
When configuring these settings, you'll need to account for your mount's inherent motor inaccuracies and environmental conditions. Temperature changes can affect motor performance, while mechanical misalignments may require additional compensation in your tracking parameters.
Update Schedule Management
Maintaining peak tracking performance depends on proper management of software updates for your telescope's motor control systems. You'll need to regularly check for and install the latest firmware and control software updates from your manufacturer to guarantee ideal tracking functionality and benefit from bug fixes.
- Schedule your updates during planned maintenance windows to avoid disrupting observation sessions.
- Keep backups of previous software versions in case you need to roll back problematic updates.
- Document all updates and subsequent testing for future reference.
Don't skip testing after updates – it's essential to verify that new software versions work correctly with your specific mount configuration.
If you encounter issues, you can quickly restore the previous version from your backup while troubleshooting. This systematic approach to update management helps prevent unexpected tracking problems during critical observation periods.
Environmental Impact on Tracking
Environmental factors directly affect telescope motor tracking performance through various mechanisms that telescope operators must understand.
Climate change's increasing impact on weather patterns can disrupt your telescope's tracking accuracy, particularly when temperatures fluctuate dramatically during observation sessions.
Your tracking system's performance also depends heavily on the power source you're using. If you're relying on non-renewable energy with unstable voltage output, you'll likely experience inconsistent motor operation.
Environmental conditions like humidity and ground contamination can affect your motor's mechanical components, leading to tracking errors. Even slight habitat disruptions around your observation site can create unexpected vibrations that interfere with precise tracking.
To maintain ideal tracking, you'll need to implement proper environmental controls and consider switching to stable, renewable power sources when possible.
Balancing Your Mount Correctly
While environmental factors pose external challenges to telescope tracking, proper mount balance forms the foundation of reliable performance. Your mount requires precise balancing of both the Right Ascension (RA) and Declination axes to prevent motor strain and guarantee smooth tracking.
- Release the RA clutch and adjust counterweights until your scope maintains a horizontal position without swinging.
- Loosen the declination clutch and adjust the telescope's position in its rings until achieving neutral balance.
- Remove cables and attach all accessories before balancing to replicate actual observing conditions.
If you're experiencing tracking issues, check for balance-related problems first. Remember to aim for "East-heavy" balance when tracking celestial objects, and regularly verify your setup as equipment changes can affect balance.
While perfect balance isn't necessary, a well-balanced mount notably improves tracking accuracy and protects your motor.
Cable Management Best Practices
Proper cable management can make or break your telescope's performance. If you don't secure your cables correctly, they'll snag during movement and interfere with your mount's tracking ability. To prevent this, anchor your cables at two strategic points and guarantee they've just enough slack for smooth operation during Meridian flips.
Use flexible cable wraps and zip ties to bundle your cables together, keeping them organized and twist-free. You'll want to create custom harnesses using available materials and clips to manage cable loops.
Make sure to plan your cable routes carefully, considering your mount's full range of motion. To reduce complexity, centralize your power and data connections through hubs, and regularly inspect your cables for wear or damage.
Regular Maintenance Schedules
Regular maintenance tasks fall into five key categories for telescope owners: daily checks, component care, drive systems, optical alignment, and preventive scheduling.
You'll need to establish a consistent routine to keep your telescope's motor tracking accurately and prevent unexpected failures.
Your maintenance schedule should include:
- Daily visual inspections and cleaning of optical surfaces
- Monthly lubrication of bearings, gears, and motor shafts
- Quarterly alignment checks and software updates
Keep detailed logs of all maintenance activities and any changes you make to your telescope's systems.
Don't wait to address problems – prompt action prevents minor issues from becoming major repairs.
Monitor your telescope's performance continuously, paying special attention to unusual noises or binding in the drive system.
Remember to store your telescope in a controlled environment to protect it from temperature variations and moisture.
Checking Gear Meshing and Backlash
Understanding gear meshing and backlash is essential for maintaining your telescope's tracking accuracy. You'll notice backlash when there's a delay in movement after changing direction, particularly between your worm gear and its driven gear.
To check for backlash issues, test your slow-motion controls. If you experience significant delays before movement starts or observe overshooting when the mount changes direction, you're dealing with excessive backlash.
While you can't eliminate it entirely, you can minimize its effects through proper adjustment and maintenance.
You'll get better tracking results by ensuring your mount is well-balanced, using your system's backlash compensation features, and regularly checking for loose components.
When changing direction, try using brief high-speed bursts to take up gear slack more effectively.
Troubleshooting Tracking Errors
When your telescope's tracking system misbehaves, several key factors could be at play. Start by examining periodic errors caused by imperfect gears and misaligned bearings, which often result in oval-shaped stars during imaging.
Environmental conditions like temperature changes and humidity can also greatly impact your mount's performance.
To effectively troubleshoot tracking issues:
- Check your mount's bearing condition and tighten any loose components that might cause sudden pointing errors.
- Verify proper RA and DEC axis alignment, as non-perpendicular axes will introduce tracking inaccuracies.
- Consider implementing autoguiding software solutions to compensate for mechanical imperfections.
Don't forget to maintain regular calibration schedules and keep your tracking software up-to-date.
For precision imaging, T-Point modeling can help create thorough error correction profiles for your specific setup.
Upgrading Mount Components
Upgrading your telescope mount's components can dramatically improve its tracking accuracy and overall performance.
Start by upgrading to higher-quality gears and motors that offer smoother, more precise movement. You'll also want to take into account replacing outdated counterweights and dovetail adapters for better stability.
Look into enhancing your mount's electronics with modern GPS and WiFi capabilities, which can greatly improve tracking precision.
If you're technically inclined, you might benefit from 3D printing custom parts or fabricating specialized components that fit your specific needs.
Don't forget to upgrade your bearings and bushings to reduce friction and noise during operation.
For better stability, add vibration suppression pads and verify all mounting rings are heavy-duty and properly adjusted.
Frequently Asked Questions
Can Tracking Issues Be Caused by Magnetic Interference From Nearby Electronics?
While magnetic interference from nearby electronics isn't typically a primary cause of tracking issues, you'll want to keep sensitive equipment isolated. Radio frequency interference can affect your computerized systems, but it's rarely the main problem.
How Do Different Telescope Focal Lengths Affect Motor Tracking Requirements?
You'll need more precise motor tracking with longer focal lengths since they magnify tracking errors. Short focal lengths are more forgiving, while longer ones demand higher accuracy to maintain clear, unblurred images.
Does Using Autoguiding Completely Eliminate the Need for Periodic Error Correction?
No, you'll still benefit from using PEC with autoguiding. While autoguiding corrects errors after they occur, PEC helps prevent them initially, reducing the workload on your autoguiding system and improving overall tracking accuracy.
Should Tracking Performance Change When Observing Objects at Different Declinations?
Yes, you'll notice tracking performance varies at different declinations. Your telescope's motor must work harder at higher declinations, and inertial changes in the optical tube can affect the drive gear's consistency and precision.
Can Atmospheric Refraction Cause Noticeable Tracking Errors Near the Horizon?
Yes, you'll notice significant tracking errors near the horizon due to atmospheric refraction. It can cause pointing errors up to 1/2 degree as light bends through varying air density layers in the atmosphere.
In Summary
Your telescope's tracking issues can be fixed through regular maintenance and proper calibration. By following alignment procedures, checking your power supply, and addressing mechanical problems promptly, you'll guarantee smooth tracking performance. Don't forget to inspect gear mesh and backlash regularly. If problems persist, consider upgrading your mount components. With proper care and attention, you'll enjoy precise tracking for years of successful stargazing.
Leave a Reply